UAW Just Agreed to Let Ford Use Technology to Monitor Assembly Workers
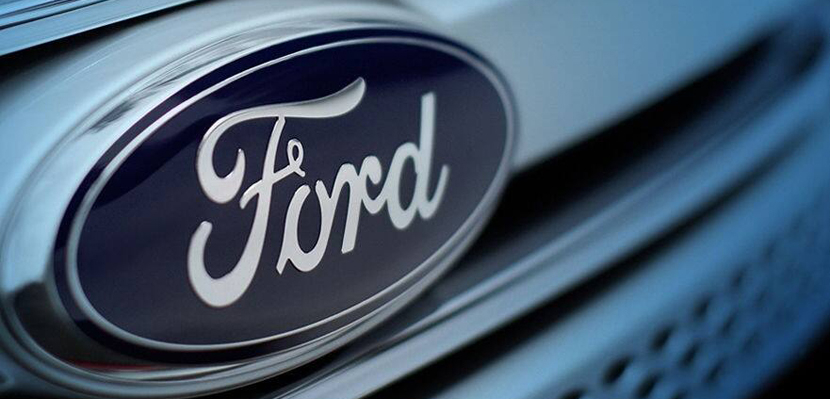
UAW's tentative agreement with Ford will allow the company to use new technologies to take time-and-motion studies to a whole new level. Photo: Ford Media Center.
Somehow it was left out of the contract highlights the United Auto Workers prepared for members: the tentative new agreement with Ford will allow the company to use new technologies to take time-and-motion studies to a whole new level.
The new language falls under the heading of “production standards” and states that the union and company will choose “pilot locations” to use new technology tools such as “digital video recording and walk path mapping devices” as well as “motion tracking systems and additional productivity implementing tools.”
On Facebook, workers discussed all the ways that management could use technology to target and harass workers and find new ways to eliminate jobs. “If we allow this kind of technology in now, there’s no telling how bad it could get by next contract... just like the tiers!” wrote one worker.
“I’m just shocked,” said Scott Houldieson, a body shop electrician at Ford’s Chicago Assembly plant. “If this is implemented, it will be like having a digital industrial engineer following your every move, trying to find new ways to speed up the pace of work and increase productivity.”
SURVEIL AND CONTROL
Similar technology is already being used by many large employers to squeeze more out of workers in hospitals, hotels, grocery stores, and parcel delivery.
Workers at Amazon’s gargantuan warehouses, for example, are expected to pack and sort hundreds of packages every hour. Amazon workers describe dehumanizing, sweatshop conditions, where people pass out from dehydration after being forced to move 250 packages an hour with no air conditioning or water.
Amazon workers are not only treated like robots, they’re also monitored by them. An investigation by The Verge found that workers were automatically fired if they failed to meet productivity standards that were monitored by an automated tracking system.
Meanwhile at UPS, “technology monitors our every move,” said Nick Perry, a delivery driver and steward in Teamsters Local 413 in Columbus, Ohio. Every day he gets into a truck loaded down with sensors that track “seatbelts, speed, exact location of the truck, exact location of our scanning device, selection time, how many times our bulkhead is open, rear door selection times, how many seconds between scanning a box until truck is started, if we followed an ‘approved’ way to drive to a stop, if we didn’t drive fast enough or if we drive too fast, and tons more stuff.”
All that surveillance is used to exert greater management control over workers, drilling them on their choices and how they spend every second.
“As a union steward I have to defend my members in the office over petty harassment about this technology,” said Perry. “Supervisors question seconds throughout our day on a daily basis to get us to stress out and speed up.”
At Ford, “the language in the agreement says the technology won’t be used as the sole basis for disciplinary action—which implies it will be used at least in part to discipline workers,” said Houldieson.
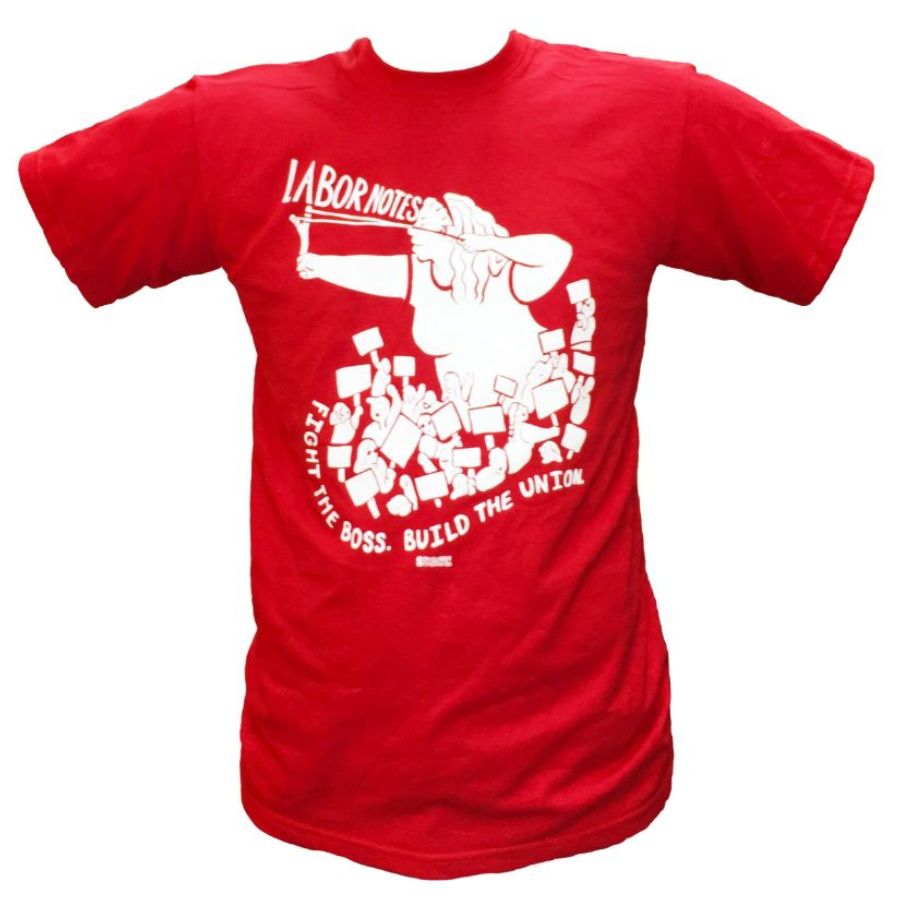
SUPPORT LABOR NOTES
BECOME A MONTHLY DONOR
Give $10 a month or more and get our "Fight the Boss, Build the Union" T-shirt.
Henry Ford was of course one of the early and enthusiastic adopters of the assembly line and of Taylorism, with its time-and-motion studies that attempted to remove all “waste” from workers’ movements on the job and to standardize their motions in machine-like fashion.
Nor is invading workers’ privacy new for Ford. In the earliest days of the company, Henry Ford established an entire department dedicated to investigating the private lives of employees to determine whether they were fit to work in his company. Workers who drank alcohol, weren’t married, or had a messy house could be fired.
PATTERN AGREEMENT
The Ford contract follows the pattern set at General Motors, where the tentative agreement passed with a 57 percent majority.
While the GM agreement did shorten the time it will take future second-tier workers to achieve top pay, from eight years down to four, they still will get no pension or retiree health benefits. And while the agreement outlined a multi-year pathway for temporary workers to achieve permanent employment, many workers were concerned about the loopholes built in—plus the fact that any temps who escape that status will simply be replaced by others. The GM agreement did not reverse the closings of Lordstown Assembly in Ohio, Warren Powertrain in Michigan, or Baltimore Powertrain in Maryland.
The Ford agreement follows the GM pattern on tiers and temps. The company announced it will be closing the Romeo Engine plant in Michigan, which employs 600 people, after ratification.
At Ford’s Chicago Assembly plant, 64 percent of the workers voted against the tentative agreement.
“There’s multiple reasons to vote against this contract, and allowing the company to use technology to monitor and discipline workers was just one more,” said Houldieson.
Voting ends November 15.
Update: November 13, 2019
The following response was provided by UAW spokesperson Brian Rothenberg to this article: “There will be no pilot project without the agreement of the local union wanting to participate in it. It cannot be used as the primary reason for discipline.”