Employers' Productivity Standards Are Not Real Science. Here's How to Push Back
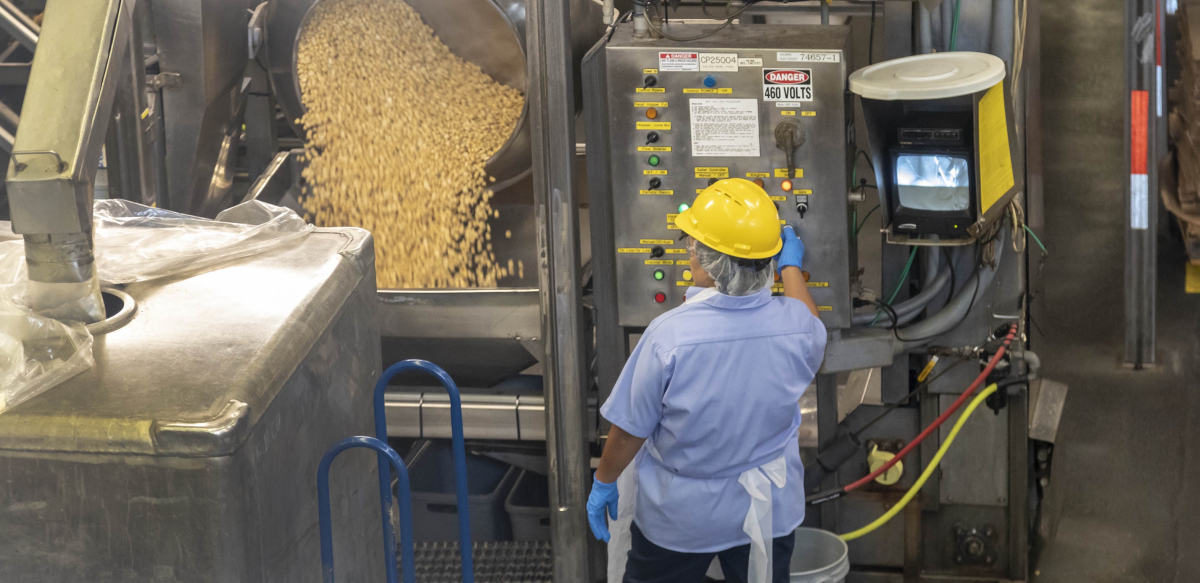
Unlike measuring temperature with a calibrated thermometer, no absolute scientific benchmark exists or can be used for work output. Photo: Jim West, jimwestphoto.com.
This article, the first in a series on how to deal with workplace monitoring technology, focuses on grievances. Future articles will discuss organizing and preparing to bargain over these issues.
Whether you’re working in a warehouse or piano factory, processing insurance claims, or taking care of patients, the use of worker productivity monitoring continues to expand.
Workplaces where jobs are monitored and measured—and workers required to meet certain performance metrics—pose a particular set of challenges for stewards.
Most historians recognize Fredrick Winslow Taylor and his 1911 book The Principles of Scientific Management as the genesis of these schemes. Taylor’s technology was basic by today’s standards: clipboards and stopwatches.
Frank and Lillian Gilbreth (of Cheaper by the Dozen fame) expanded on this by using frame-by-frame film study of workers performing tasks with a specially calibrated “microchronometer,” documenting worker micro-motions and the time they took.
More recently, with the tremendous growth in computing power and data collection, the ability to use technology to gather data about workers is ubiquitous, and bosses are eager to use these tools to maximize productivity and profits.
Today, most production targets heavily involve computers collecting data and computing efficiency metrics. Regardless of the specific details, all systems use the concept of “normal” time (the time needed for a normal worker performing at 100 percent pace), and then convert it to a “standard” time by adding time for personal needs, fatigue, and unavoidable delay (PFD).
This multiplier purports to account for the need to use the restroom, allow for the effect of physical, mental, and environmental fatigue, and reflect unexpected delays in the normal routine.
GRIEVE AND…
Beyond struggling to understand how these opaque, computerized systems evaluate people, a steward must assess member feedback and decide how best to proceed with practical actions and grievances.
If the broader goal is to constrain or eliminate these systems, that will require collective action and bargaining. But until that happens, filing a grievance can be good tactically when it helps you get management’s attention to address workplace issues.
The union’s strongest position is generally to grieve to defend members from any discipline or adverse consequences—shifting the burden of proof to the company and invoking the principles of just cause.
GET SPECIFIC
Often when workers feel that the effort required to meet the standard is unreasonable or has changed, they will approach their steward to file a grievance.
Workers may feel the standards are too demanding generally. But in investigating a grievance, it’s important to dig deeper.
Are the standards unreasonable in specific areas? For certain tasks? Under particular conditions? At precise times? Probing deeper can help identify the root cause of the problem and build a stronger case for winning a grievance.
TYPES OF GRIEVANCE
Knowing and understanding any existing contract language is essential in forming a strategy. These general guidelines can help you navigate the issue where the contract is silent.
Three common causes of problems with standards are:
Non-standard or missing work: Extra work is being done that was not included in the original calculation of the standards.
For example, if there is a change in the process or duties mandated by supervisors on the fly, then the time to perform this must be added.
Consider a process that requires printing and applying labels from a 500-piece roll. If that roll runs out twice each shift and the operator is responsible for loading and maintaining the label printer (a non-cyclic element in engineering jargon, meaning it happens periodically, but not every time you repeat the cycle), the time required for this must be included.
Deterioration of standard conditions: Determine where and under what conditions the standards were developed, and document differences between then and conditions now.
For example, in a warehouse, there may be periods when seasonal items in high demand cause excessive delays because of increased congestion in the aisles where these items are stored.
A potential solution would be to negotiate a temporary reduction in the performance level at which the standards are enforced or to increase the delay allowance.
Inadequate PFD allowances: These allowances are multipliers that directly increase how much time is added to normal time to calculate the standard. So the larger the allowance, the more time will be allowed.
Companies tend to be very optimistic in estimating them, setting them as low as possible.
For example, say that the normal time for making a pot of coffee is 120 seconds. Does that mean you can make 30 pots an hour?
A default recommendation in engineering textbooks is to use a 15 percent PFD allowance. In this case, a reasonable standard would be to add 15 percent (or 18 seconds) for each cycle. Adding this allowance time to the “normal” time sets the bar to make 26 pots of coffee an hour, not 30.
Especially for delay allowances, it can be helpful to document the actual delays experienced. Members can get involved by gathering data in logs or tracking a random sample of orders spread over time. It is essential to make the company explain how it determines its allowances.
INFORMATION REQUESTS
As with any potential grievance, a thorough investigation is required.
Information rights are one area of labor law that remains solidly pro-union. You can use the right to information to gather data to help win grievances and put the boss on notice and apply pressure toward an acceptable resolution.
In addition to the information requests that you would typically submit to understand a situation better and bolster your just-cause arguments (documentation that substantiates the company position, past discipline, prior performance, training records, etc.), you also need to learn about the company’s method of determining the standard.
Once we understand the company’s approach, we can base positions on evidence that its work measurement technique is inappropriate or has been misapplied.
As a baseline, request the procedure by which the company established its standard. What is the system, how does it determine the times allowed, and what parts of the work are included?
Who has access to the system, when and how are changes made, how are they documented, and what changes have been made during the time frame of your interest?
Also, request the procedure by which the company established its personal, fatigue, and delay allowance. Often you can critique the company’s numbers by demonstrating the flaws in deriving them and the unreasonableness of doing the job as outlined in the fatigue calculations.
Ask management to produce published studies or documentation used to determine their fatigue allowance. Sometimes this will demonstrate that these allowances are based on subjective judgments or entirely made up rather than scientific.
If the company stalls or refuses to provide this information, filing a National Labor Relations Board complaint is free, and in most cases, you can expect a positive result. Plus, the company will be forced to spend time and energy defending itself. Ultimately you get the information you need and set a precedent that compliance with information requests isn’t optional.
IT’S NOT HARD SCIENCE
It’s important to remember that, even if your employer shows you some official-looking computer printouts, there is plenty of room for error.
While there is an accepted standards methodology, standards are not scientific or “accurate” in any absolute sense. Unlike measuring temperature with a calibrated thermometer, no absolute scientific benchmark exists or can be used for work output.
This is true of all work measurement techniques. They each depend on subjective judgments in different phases of their application—from determining what the “normal” time should be to what allowances should be made for PFD. As such, we should avoid using words like “accurate.” Instead, discuss standards as being either acceptable or unacceptable to the people who work under them.
Remember that discussions about standards are, in essence, bargaining. As anyone who has been part of a bargaining team knows, you don’t get what you deserve—you get what you can win.
Establish your bottom line and make requests that go beyond it. To avoid getting bogged down on minor details, keep in mind your ultimate goal and take actions that progress toward it.
Michael Childers is a professor at the University of Wisconsin-Madison School for Workers.
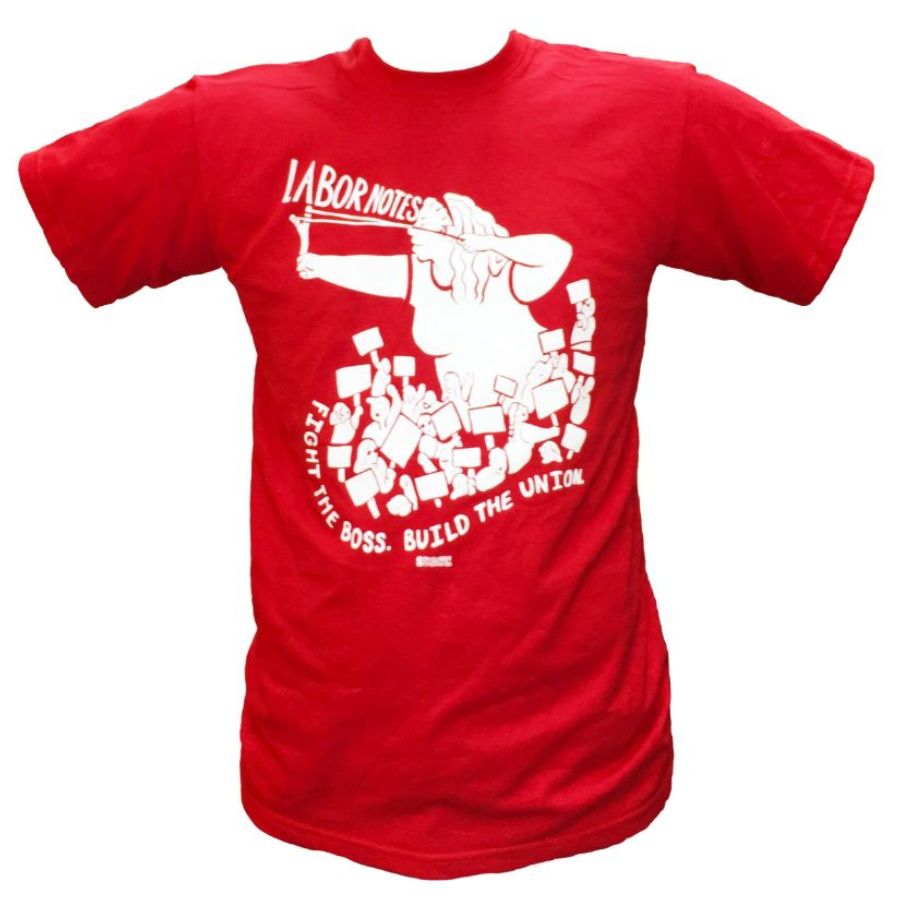
SUPPORT LABOR NOTES
BECOME A MONTHLY DONOR
Give $10 a month or more and get our "Fight the Boss, Build the Union" T-shirt.